In recent years, the price of petrochemical energy, especially coal, has been gradually rising. The ensuing tests make the cement industry realize that energy saving and carbon reduction are not only a cost issue for enterprises, but also related to the future development and survival of enterprises. Under the new situation and environment, cement industry continues to promote the transformation of enterprise energy saving and consumption reduction, and explore the new process and new technology to reduce carbon, it is imminent. Relevant research and development teams are studying how to reduce the proportion of petrochemical energy use and improve energy efficiency through new technologies and processes to reduce carbon intensity. And in cement manufacturing process, production technology and energy utilization are twin topics. The heat concentration of rotary kiln is the core to improve the temperature of the firing zone. The heat of pulverized coal should be exerted in the firing zone as much as possible.The pulverized coal combustion efficiency is the key to affect the fire concentration of rotary kiln.
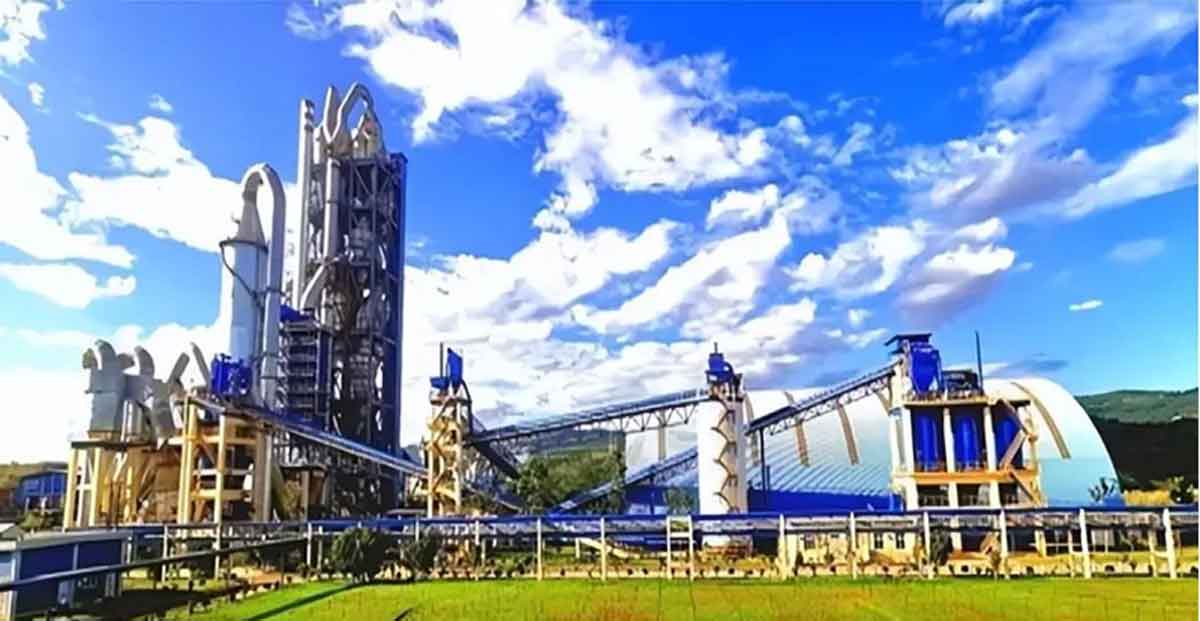
At present, there are some problems in the sintering system, such as poor raw material flammability, low heat exchange efficiency, serious air leakage, large heat loss, large system resistance, high power consumption and unstable thermal system. To promote the health and energy saving of the firing system, it can be achieved by increasing the calorific value of coal, increasing the heating rate and forging firing temperature in the kiln, and increasing the secondary air temperature. The whole insulation body will play an important role in improving the energy efficiency, increasing the heating rate and forging firing temperature in the kiln, increasing the secondary air temperature and reducing the heat loss.The traditional thermal insulation materials in cement industry are microporous calcium silicate board or ceramic fiberboard, which have a thermal conductivity of 0.15W/(m·K), and their thermal insulation performance can no longer meet the needs of heat insulation and energy saving in sintering system. Simply stacking thermal insulation materials cannot solve the fundamental problem. The temperature of different parts of the production equipment is not the same. The economy, safety and timeliness of simply stacking thermal insulation materials are not considered.The correct approach should be different insulation material design for different sections.
The Low Temperature Part:
the traditional calcium silicate board has been able to achieve the required thermal insulation effect, from the economic point of view, can consider only calcium silicate board.
In Non-Ultra-High Temperature Parts:
the combination structure of high temperature nano microporous panel and calcium silicate plate can be used, which can not only achieve the effect of cooling more than 20℃ but also ensure the economy. When the nano microporous panels are placed behind castable or firebrick during construction, the high-temperature nanoplates provide better insulation than the calcium silicate panels on the hot surface.
Ultra-High Temperature Parts:
We can use the combination of high aluminum ceramic fiber board, high temperature nano heat insulation panels, calcium silicate board, can not only ensure the heat insulation effect, but also to ensure the safety of heat insulation materials, timeliness. 4. For surfaces and pipes that need to be insulated, flexible nano insulation blanket mat can be used to closely fit surfaces and pipes to achieve the best thermal insulation effect.
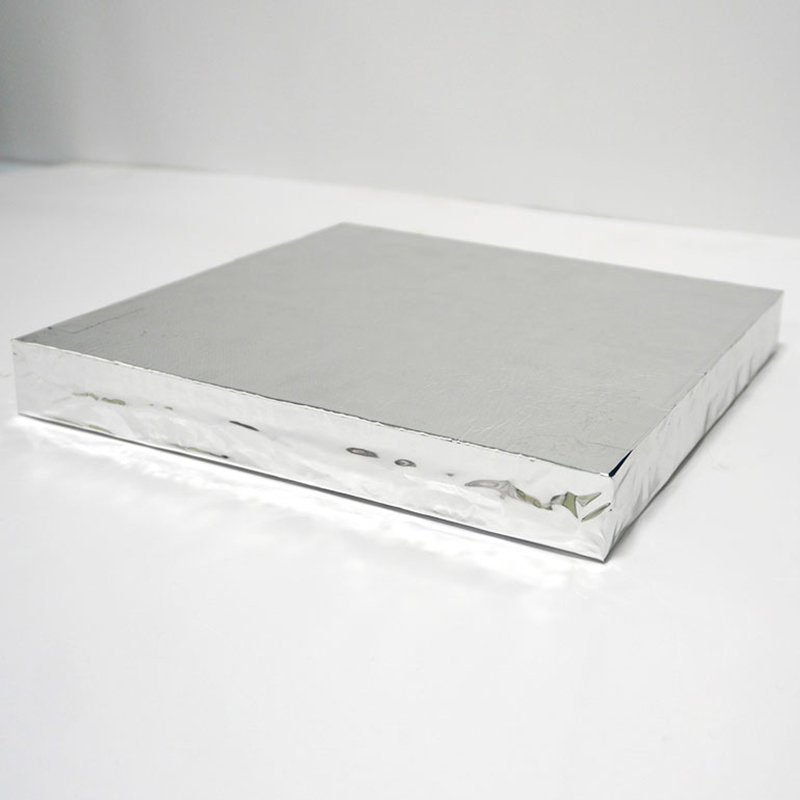
High Temperature Nano Microporous Panel Advantages As Follows:
Very low thermal conductivity, 800℃ thermal conductivity 0.03W/(m·K)
The maximum operating temperature can be 1150℃
Stable high temperature line shrinkage,Very low heat storage value
Easy to cut and install,Product packaging is diversified

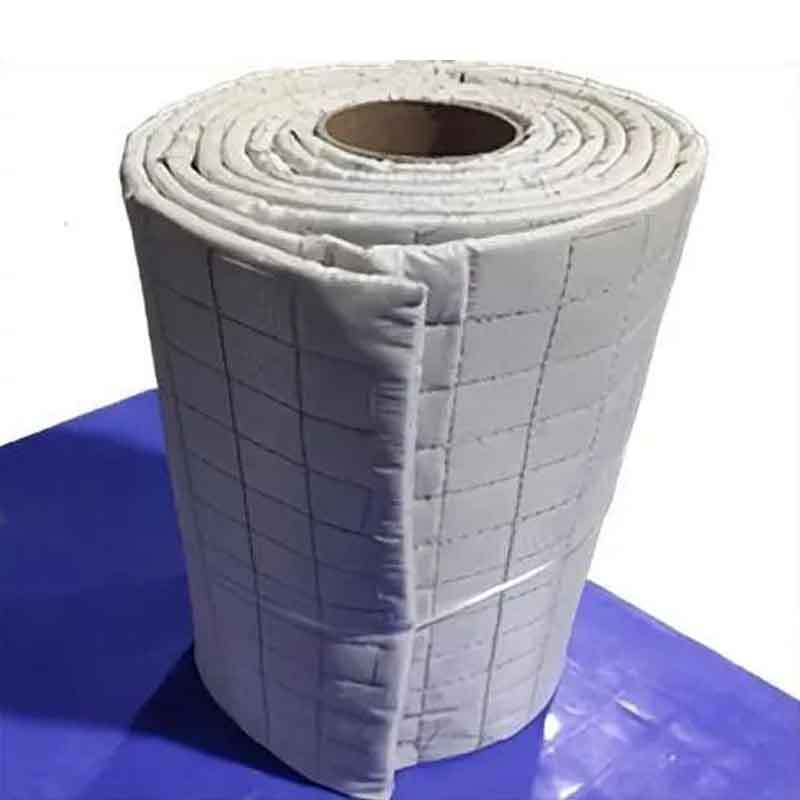
High Temperature Flexible Nano Insulation Blanket Mat Advantages As Follow:
Extremely low thickness to achieve excellent thermal insulation effect, 800℃ thermal conductivity 0.042W/(m·K);
Long-term use temperature can reach 1050℃;
Stable high temperature performance;
Construction convenience of arbitrary cutting;
Can be supplemented by hate water treatment, to meet the construction performance of special customers;
According to customer requirements can design complex shaped parts.
According to industry estimates, the use of high temperature nano insulation materials can provide a space for reducing the heat consumption of 2~3 kg standard coal per ton of clinker, effectively improving the heat utilization efficiency of cement production line. Compared with the traditional calcium silicate plate, the new nano thermal insulation material can reduce the external surface temperature of the preheat decomposition system equipment by 8~15℃ when the thickness is the same. After the new nano insulation material insulation modification, the equipment shell temperature has a lot of room to reduce. To reduce the loss of energy in the production link and reduce energy consumption, the corresponding economic effect of saving coal is very significant, and greatly reduce carbon emissions.
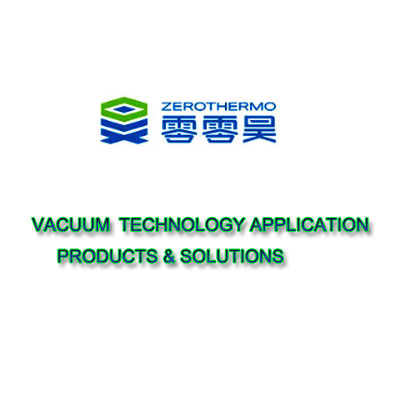
Zerothermo focus on vacuum technology for more than 20 years, our main products : vacuum insulation panels based on fumed silica core material for vaccine, medical, cold chain logistics, freezer, integrated vacuum insulation and decoration panel, vacuum glass, vacuum insulated doors and windows. If you want to learn more information about Zerothermo vacuum insulation panels, please feel free to contact us, also you are welcome to visit to our factory.
Sale Manager: Mike Xu
Phone :+86 13378245612/13880795380
E-mail:mike@zerothermo.com
Website:https://www.zerothermovip.com
Post time: Dec-06-2022